2018-07-24T12:00:00.0000000+01:00
July 24, 2018
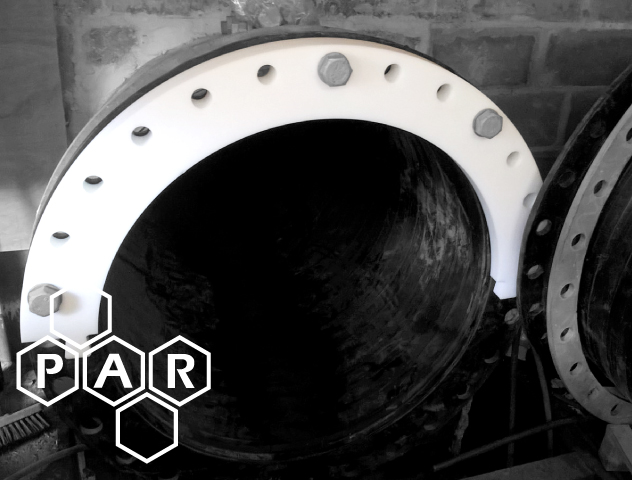
PAR Group are one of the UK’s foremost plastic machining companies and machine engineering plastic components using advanced CNC technology. We have the capability to manufacture parts from simple to highly complex shapes. Our plastic machining facilities include CNC machining, cutting, routing, turning, drilling and milling. Our experienced engineers and CAD technology allows us to precision engineer components to existing samples or drawings and in a range of material types.
The Project
A specialist company dealing in water based engineering had two identical flanges on a pipeline which were required to meet and join. The inlet pipe coming through the wall was angled backwards and fixed, causing the flange to point upwards. This meant that when the flanges met at the bottom, there was still a considerable gap (roughly 50mm) at the top, restricting the flanges from meeting.
The Solution
Due to the inconsistency of the gap, we were required to produce a gasket with a taper. To achieve the angle required, the part had to be machined out of a rigid plastic as opposed to a typical gasket material. This was achieved at our Manchester branch using our 5-axis CNC technology. As we were restricted by the sheet size of the plastic, the gasket had to be machined in two parts with dovetails to join them together. The gasket was installed on-site and sealed successfully between the flanges.
The Benefits
Avoided the significant cost of replacing or re-locating the misaligned pipework.
Key Features
• Bespoke manufactured as required.
• Manufactured wholly in-house.
• CAD drawings taken for ease of re-order.
• Successfully sealed misalligned pipework.
• Dovetailed joints fitted together accurately.
You can find out more about our plastic machining capabilities here.
Tapered Gasket
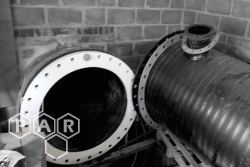
Tapered Gasket Sealed
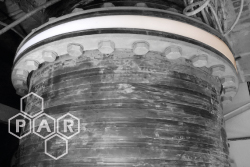